Our casing desalting and washing machines, in LVA and LVE versions, are used to desalt and wash casings stored in salt. They are made entirely of stainless steel and consist of a pentagonal mesh tank with a desalting and rinsing shower and a washing tank.
The capacity is one, or half a 250-l drum, respectively.
The product is manually introduced into the pentagonal tank made of a specially made net, so as to ensure proper de-salting of the product. The tank rotates under a shower to remove the salt on the outside of the casings. At the end of desalting, the tank is filled with water at the right temperature and with the normally used cleaner, with restart of the tank carrying out the casing washing. After the tank is emptied, a short rinsing cycle, which can be avoided with natural detergents, ends the treatment cycle.
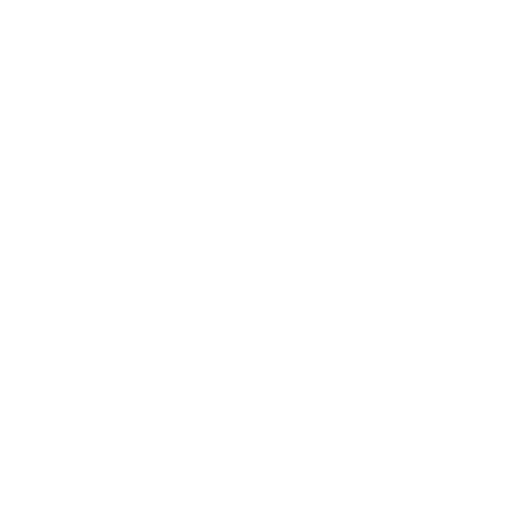
Programming through operator panel
Programming is done through an operator panel; thus, it is possible to adjust treatment times, rotation speeds and other parameters that can be stored in individual recipes. The optimization of recipes according to the type of casing and its origin allows a constant percentage of salt in the casings, to the advantage of the quality and homogeneity of the cured product.
Our casing washers make it possible to have casings ready for use in less than an hour, with considerable reduction in the storage of washed product ready for production, that is to say, with reduced space required,less labor and reduced water consumption compared to traditional desalting systems, carried out in tanks with disposable water for 24 hours or more.