The TFRC system for loading and unloading hung deli meats, on trolleys, frames, trees or suspended conveyors, even of great height, can handle different products at the same time, coming from semi-automatic loaders, from automatic loaders, or taken from frames from production areas where manual loading is limited to the easiest level.
The same system is part of our system for the automatic hooking and unhooking of bellies for bacon.
It is possible to pick up all the bars of an entire level; optimal acceleration management allows high speeds with very little oscillation of the products, with high throughput without products dropping.
It is able to handle frames of great height and handled by AGVs and of suspended tray conveyors. When unloading, it is also possible to transfer one pole at a time to the packing or peeling lines, even with automatic bar extraction or loop cutting.
The special design mode, protected by international patents, reduces the cross-sectional footprint of the system (only 300 mm more than the length of the frames to be loaded or unloaded); it is the most compact and easiest system to fit into existing production facilities.
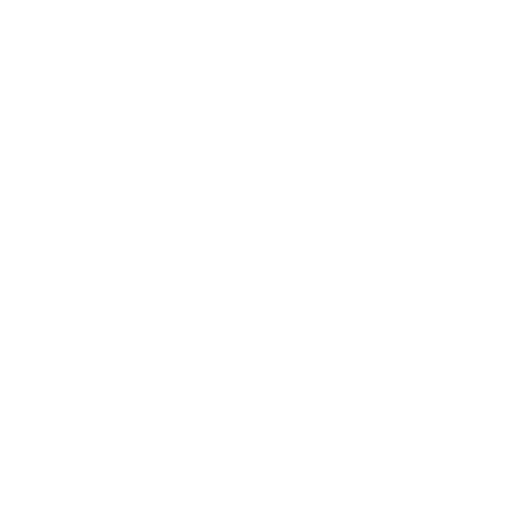
Operator panel for system management
Thanks to the advanced TFRC software, it adapts to the irregularities of existing frames, which are often not made for automation; our system is characterized by a very high precision of movements that allows managing the insertion into the frames of bars even with very limited dimensional tolerances. An operator panel makes it easy to manage the system, and remote technical assistance is available.
Benefits
- Reduced labor for hanging and unloading
- Reduction in employee turnover
- Reduction in strenuous and repetitive work
- Reduction in occupational injuries and illnesses
- Increased loading capacity of bars and frames
Key features
- FLEXIBILITY OF DESIGN: the system is specifically designed to be used within existing production units as well
- ADAPTABILITY: there is no need to change frames and bars
- COMPACTNESS: the least bulky on the market, it fits into most existing production facilities
- MODULAR: can be easily adapted to production needs and expanded as the business grows
- FLEXIBLE: it can work with products having different dimensional characteristics, even simultaneously and be fed by manual or automatic units, even simultaneously
- POWERFUL: one unit can be fed simultaneously by two automatic bar inserting machines
- LOW MAINTENANCE COSTS: robust construction, axis controls used minimize mechanical stresses making the systems intrinsically reliable
- SANITIZATION: easier washing and cleaning due to the design and location of the most sensitive components.